-
×InformationNeed Windows 11 help?Check documents on compatibility, FAQs, upgrade information and available fixes.
Windows 11 Support Center. -
-
×InformationNeed Windows 11 help?Check documents on compatibility, FAQs, upgrade information and available fixes.
Windows 11 Support Center. -
- HP Community
- Archived Topics
- Notebooks Archive
- Problem with Pavilion dv8 top slider bar (treble/bass contro...
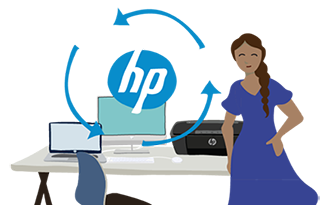
Create an account on the HP Community to personalize your profile and ask a question

02-08-2011 10:03 AM
That is good news since it is the exact same result that I had. This really does point to a static grounding issue and I already have a solution in place that I am in the process of testing.
On your laptop, does the mute and wifi turn off and on if you press just above the F9 key, but not on a touch button? This also will stop my touch buttons from firing off as long as I am pressing on it.
Does anyone not have a Blueray/DVD combo drive that is experiencing this issue?
Thanks,
Brian
02-08-2011 11:33 AM
I don't know if I have Blueray - but I don't think so. Sorry to be so dumb about this, but how could i tell since I don't remember what I ordered...short of trying to play a Blueray dvd, which I don't have.
Sandy Lynn
02-08-2011 10:49 PM
Problem Solved!!!!!!!!!!!
I just finished putting it back together and it works perfectly! On my system it was very easy to test because when I pushed just above the F9 key the mute and Wifi would go crazy %100 percent of the time. Well, it does not malfunction, no matter where I press or how hard. I can press any of the capacitive touch buttons without any issues for the first time ever.
There are two parts to the problem. The first is the static grounding and shielding. The second is the exposed metal end caps of the LIF connector. This is the connector that the ribbon cable plugs into on the LED board. When I pressed on the LED before the revision, the exposed metal case of the connector would transfer the static charge to the housing just below it and cause a misfire of the cap touch circuit, triggering an actuation when it was not desired. This also occured randomly when the static charge potential reached high enough levels and jumped to ground also causing an unwanted actuation.
The solution was to shield the ribbon cable with high temp thin foil tape and increase the surface area of the existing foil tape ground pad that it rests on. I also secured the ribbon cable to the ground pad with additional strips of foil tape. Next I covered the LIF connector with Kapton tape to insulate it but left enough room to still plug the cable in. Once the metal connector housing was insulated I placed thin strips of foil tape over it still leaving the connector open for the ribbon cable. A good reference to use is the plastic slide lock that is pushed in to secure the end of the cable to the LIF. Cover only the plastic/metal housing of the LIF but not the slide lock or else you will not be able to secure the cable into the connector. Cover the kapton with foil tape to shield and ground it. You also do onto want to cause anything to short out on the foil tape that is being added.
The idea of taping the ribbon cable down to the existing small section of foil shielding is not a new idea but the exposed metal end caps of the LIF has not been mentioned. This is the main reason that most people have failed when performing the "tape down" method of the cable to the foil ground pad. My cable was actually secured well to the pad with adhesive. The only problem was that the shielding on the cable was not long enough and the ends of the LIF (low insertion force) connector where exposed.
I also placed some shielding on the under side of the entire cap touch board (LED board) and over the round mini sub woofer as well as wrapping the power and wifi harness to limit the EMI to the cap touch board (LED board). This can be done by placing foil tape over the channel that the wire harnesses reside in. I am not sure how much the shielding over the harness really had because usually that kind of problem causes a lack of response and not auto actuation. The foil tape shielding that I placed on the under side of the LED board did help to provide a nice path to ground for any residual static charge so I would be sure to include that step but you can likely omit the harness wrap.
After taking X-rays of the LED board I could see that the design and fab was actually very good so that left the static issue. performing the above will resolve the problem as long as you do not have some other underlying issue such as a defective LED board or power supply. After finding the cause I can almost for certain conclude that the Blu-Ray drive is not part of the problem.
On another note, I found a lot of loose screws and adding in the thin layers of foil tape made the entire keyboard and LED button panel feel much more robust and rigid. Almost as if it was designed correctly. Unfortunately the loose screws did not end up being the cause of the problem nor did the flexing of the LED board. This is ruled out due to the fact that I could trigger a false actuation without coming in direct contact with the panel. Just getting close enough to it with the tip of my finger would cause it to go nuts, all with no actual load being applied to the assembly.
That is all I can include for tonight but I will post some more info later. I did not take any pictures since I had planned on taking it apart again not expecting to fix it on the first try.
I am looking into trying to design & manufacture a kit that would come with die cut shielding gaskets or at least put out the info for anyone that wants to get the capacitive touch buttons working once and for all. It is not very hard to apply the foil tape but it is not fool proof since everyone may interpret and apply the fix differently. The goal is to put out a kit as well as the needed information that would allow a repeatable retrofit.
The panels are a little scary to take off since you feel like they are going to break but they do come off with a little patience.
Let me know what everyone thinks.
Thanks,
Brian
02-10-2011 03:22 PM
That is actually good news. It helps to confirm that the condition that causes the buttons to malfunction is related to the build up of static and the exposed metal ends of the LIF connector as described in my last post.
If you follow my repair instructions it will end your capacitive touch button issues. Unlike other solutions, this fixes the cause of the problem and does not disable the buttons. My laptop is still working perfectly with no malfunction of the touch buttons since I added the ground and shielding to the LED board (touch button) as well as insulating the exposed ribbon cable connector.
I can push right above the F9 key and it does not go crazy anymore. Its amazing! Since my fix worked it also rules out the charger & DVD/Bluray drive as the cause.
Add some high temp foil tape along the bottom of the LED board and cover the ribbon cable connector with some kapton tape or suitable insulating tape. Add some foil tape around the existing foil ground pad that is under the ribbon cable and wrap additional foil tape around the ribbon cable. You will see foil tape on the ribbon cable already and you want to try to extend the coverage towards each end of the cable but not too close to the exposed motherboard or the LIF connector.
The goal is to provide a path to ground for the foil that you add to the underside of the LED board. To do this just make sure that when the board is installed that it has some foil ground on the plastic base that connects to some of the existing ground foil. The design rule is that all conductive parts should always be grounded and never isolated. That is why you will notice that the speaker grill has foil ground tape at some of the mounting screw holes. Use those to connect the additional foil to and you will have a good ground path.
The extra foil may not even be needed. I did it to ensure I covered all possible causes. just covering the exposed LIF connector may also fix the problem since that is where the static is discharging to the base. You still have to take the speaker grill, keyboard and LED board out so its easy to do while you in there.
02-14-2011 11:33 AM
Brian,
I still don't have my laptop back from HP so don't know if they have figured out the static issue. I am glad that you seem to have remedied the problem but I'm nervous about opening up my computer. The most I've ever done is replace a keyboard and that was on an old hand-me-down laptop -- not a brand new $1500 dollar one. Are you still planning on including some pictures or step-by-step instructions? If you do decide to put together a kit with dies, etc. I would be interested.
02-14-2011 05:29 PM - edited 02-14-2011 05:31 PM
@ puddinck
http://h20574.www2.hp.com/default.htm?lang=en&cc=US&hpappid=psml
Give the library time to load as well as the video page, you will know what I mean when you get there.
I found the speaker cover to be the trickiest part to remove as the snaps underneath can be a bit of a bear to release.
02-14-2011 10:02 PM
Yes, I will try to put up some pics of the added foil and kapton. Once you get it apart you will have no trouble getting it to work once and for all. The video links above from HaggisCat are a huge help.
Putting it back together I noticed that I had to work my way around the panels a few times pressing with my finger tips to get everything to snap into place just right. It wasn't too bad. The worst case is that you snap a plastic tab but you can always get the plastic kit from HP that has almost everything that you would need to replace. The speaker grill may be separate.
This would be a very hard repair if the laptop was 6 years old or more because the plastic would be very brittle and would crack very easily. On a 1~2 year old system the plastic is still easy enough to work with.
02-23-2011 06:38 AM
Hi Brian220x,
Any luck with posting pictures. I am anxious to follow your instructions and finally get this repaired, but would like to see some pictures of the finished product before proceeding. Only looking for pictures of the final foil wrap and tape wrap.
Thanks
